Zement
Prozessoptimierung und hohe Ansprüche an die Qualität von Produktion und Produkt setzen Maßstäbe.
Einer der wichtigsten Werkstoffe der Welt
Zement ist das Bindemittel, das dem Beton seine wesentlichen Eigenschaften verleiht: Festigkeit und Dauerhaftigkeit. Vermischt mit Wasser erhärtet der Zement zu festem Stein und verbindet die Gesteinskörnung auch unter Wasser miteinander. Schon die Baumeister der römischen Antike kannten das Prinzip und schufen mit ihrem Opus Caementitium Bauwerke wie das Pantheon in Rom, die Jahrtausende überdauerten und noch heute faszinieren.
Doch erst die Entwicklung des modernen Zements im 19. Jahrhundert ermöglichte den Siegeszug des Betons und verhalf ihm zum Titel „Jahrhundertbaustoff“. Zement wurde so bis heute zum meistverwendeten Industrieprodukt der Welt. Die Zementproduktion beträgt weltweit ca.
Ausgangsstoffe zur Portlandklinkerproduktion
Der fertige Portlandzement besteht in der Hauptsache aus Calciumsilicaten und Calciumaluminaten. Die Ausgangsstoffe zur Herstellung des Portlandzements müssen hauptsächlich Calciumcarbonat (CaCO3) und Siliciumdioxid (SiO2) sowie in geringen Mengen Aluminiumoxid und Eisenoxid enthalten. Zu den Gesteinen, die diese Verbindungen liefern, gehören Kalkstein und Ton, die meist getrennt abgebaut und danach im geeigneten Verhältnis gemischt werden, aber auch als Mergel natürlich gemischt vorliegen.
Temperaturen von 1.450 °C
Damit aus diesen Ausgangsstoffen Portlandzementklinker entsteht, müssen sie im Drehofen bei sehr hohen Temperaturen um
Umweltfreundliche Produktionsverfahren
Die deutsche Zementindustrie verfolgt schon seit Beginn des 20. Jahrhunderts zielstrebig Konzepte, CO2-Emissionen und den Einsatz thermischer und elektrischer Energien zu reduzieren. Dabei werden drei ineinander greifende Ansätze verfolgt
- Reduzierung des Anteils des Portlandzementklinkers im Zement durch Verwendung alternativer Ausgangsstoffe
- Steigerung der Energieeffizienz durch Verbesserung der Verfahrenstechnik
- Ersatz fossiler Brennstoffe durch den Einsatz alternativer Brennstoffe
Klinkereffiziente Zemente reduzieren CO2-Footprint
Durch die Verwendung weiterer hochwertiger Einsatzstoffe bei der Zementmahlung werden nicht nur natürliche Rohstoffvorkommen geschont, sondern vor allem der Klinkergehalt im Zement reduziert und dadurch der Brennstoffverbrauch und die CO2-Emissionen verringert. In erster Linie kommen in Deutschland neben Klinker als Hauptbestandteile im Zement Hüttensand und ungebrannter Kalkstein sowie in geringerem Maße Flugasche, natürliche Puzzolane oder gebrannter Ölschiefer zum Einsatz. Auf diese Weise ist es gelungen, den so genannten Klinkerzementfaktor in Deutschland von
Heute bestehen mehr als
Investitionen in Umweltschutz und Energieeffizienz
Durch hohe Investitionen in Anlagentechnik hat die Zementindustrie ihre Umweltperformance konsequent verbessert. Der Anlageneffizienzgrad liegt heute bei rund
Die Entwicklung moderner Mahlverfahren, in denen der aus dem Ofen tretende grobkörnige Zementklinker zum staubfeinen Zement gemahlen wird, erlaubt zudem eine erhebliche Verringerung des Bedarfs an elektrischer Energie.
Fakt ist:
1.
Mit mehr als 70 % lag der
2.
Im Durchschnitt haben die deutschen Zementwerke ihren thermischen Energiebedarf seit den 1950er Jahren um
3.
Die deutsche Zementindustrie hat ihre energiebedingten CO2-Emissionen (Strom + Brennstoff) in den letzten 20 Jahren drastisch verringert.
4.
Weltweit werden rd. 25 % der CO2-Emissionen der Zementherstellung durch die Carbonatisierung von Beton und Mörtel im Laufe ihrer Lebensdauer gebunden.
5.
Heute wird deutschlandweit bereits 65 % der Brennstoffenergie durch alternative Brennstoffe gedeckt – das ist mehr als eine Verdopplung im Vergleich zum Jahr 2000.
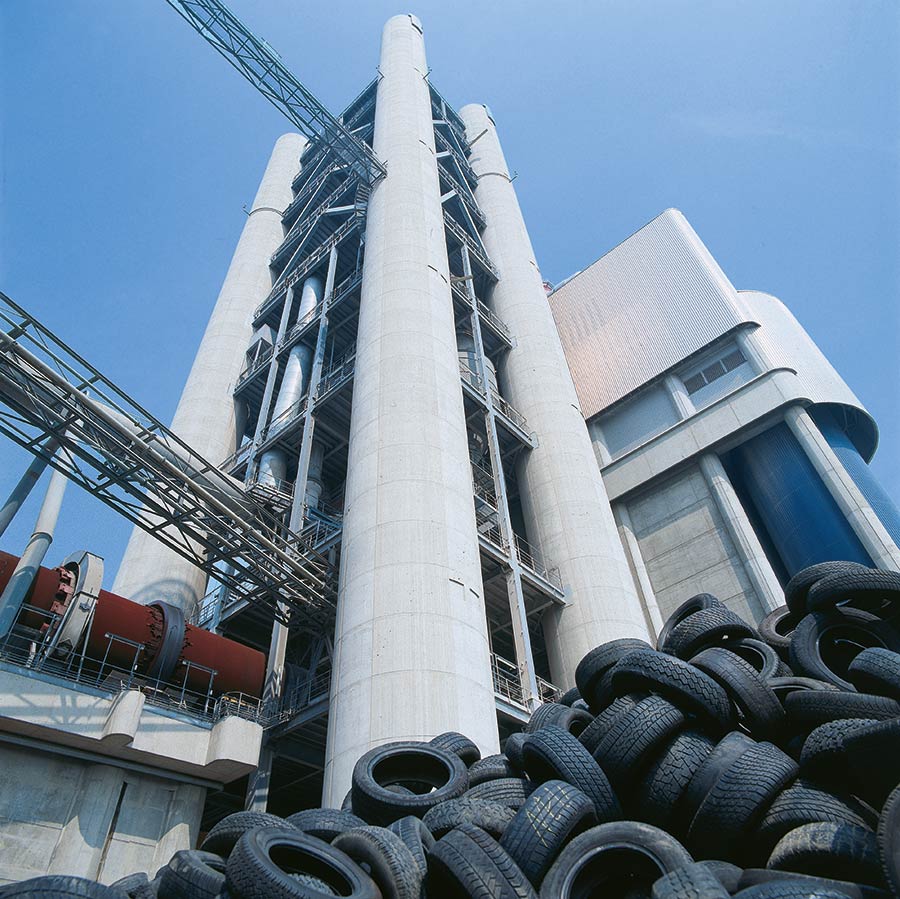
Etwa die Hälfte aller in Deutschland anfallenden Altreifen wird in der Zementindustrie als Energieträger und Rohstofflieferant verwertet. Die bei der Verbrennung entstehenden Aschen und Stahlkarkassen werden als notwendige Rohmaterialbestandteile in den Portlandzementklinker eingebunden.
Foto: Verlag Bau+Technik GmbH
Ersatz fossiler Energieträger durch alternative Brennstoffe
Einen wichtigen Beitrag für die Verringerung der Treibhausgasemissionen in der Zementindustrie leistet auch der Ersatz fossiler Energieträger durch alternative Brennstoffe, die zum Teil einen hohen Gehalt an Biomasse aufweisen. Der Anteil fossiler Brennstoffe (vor allem Braun- und Steinkohle) wurde von ca.
Umweltfreundliche Verwertung statt Deponierung
Diese leistet nicht nur einen Beitrag zur Einsparung fossiler Energieträger. Die alternativen Brennstoffe, die sonst anderweitig entsorgt werden müssten, werden hier besonders sicher verbrannt. Drehofenanlagen der Zementindustrie unterscheiden sich von klassischen Feuerungsanlagen in erster Linie durch die Verbrennungsbedingungen beim Klinkerbrennen. Brenngut und Drehofenabgase werden im Gegenstrom geführt und intensiv durchmischt. Temperaturverlauf und Gasverweilzeit in Drehöfen bieten daher besonders günstige Bedingungen, um organische Verbindungen, die über Brennstoffe eingetragen werden oder daraus entstehen, vollständig zu zerstören. Die verbleibenden Verbrennungsaschen der Ofenfeuerung werden zum mineralischen Bestandteil des Zements und müssen daher nicht entsorgt werden.
CEMBUREAU, die Vereinigung der europäischen Zementhersteller, hat dem europäischen Parlament eine „low carbon roadmap 2050“ vorgestellt: Demnach können die CO2-Emissionen bei der Zementherstellung durch konventionelle Maßnahmen bis 2050 um bis zu
- Ressourceneffizienz durch Einsatz alternativer Brennstoffe
- Energieeffizienz durch Ersatz älterer Produktionsstätten durch moderne Werke und durch kontinuierliche Modernisierung der Anlagen.
- CO2-Abscheidung im Zementwerk und industrielle Verwertung bzw. Speicherung
- Produkteffizienz durch Zemente hoher Leistungsfähigkeit, die eine geringere Zementmenge pro Kubikmeter Beton erlauben, und Hochleistungsbetone, die schlankere Bauteile mit weniger Masse ermöglichen.
- Effizienz der Gebäude aus Beton durch optimale Nutzung der guten bauphysikalischen Eigenschaften des Baustoffs und dessen Dauerhaftigkeit, Betonrecycling und „CO2-Verbrauch“ durch Carbonatisierung.
Zementherstellung
Bildnachweis (von oben): Verein Deutscher Zementwerke e. V. (VDZ) | HeidelbergCement AG / Steffen Fuchs